Одним из факторов, препятствующих кристаллизации сахарозы из утфелей, является та часть несахаров сахарной свёклы, которая не удаляется в процессе очистки соков и накапливается в мелассе,
удерживая в ней и значительное количество сахарозы. Эта несахаристая часть представлена многими веществами, обладающими различной мелассобразующей способностью, повышающими вязкость и цветность продуктов, но наиболее «вредными» являются соединения щелочных и щелочноземельных металлов. При этом на коэффициент мелассообразования данных металлов влияет не только их количественное содержание, но также характер и заряд анионов, с которыми они связаны в растворе. Ввиду высокой растворимости удаление их химическим путём в условиях сахарного производства представляет сложную задачу. И наиболее эффективным решением проблемы обессахаривания мелассы являются способы ионного разделения.
В настоящее время на территории стран Таможенного союза функционируют два предприятия по обессахариванию мелассы методом хроматографической сепарации. Однако практические результаты их работы не являются предметом широкого доступа и не позволяют объективно судить об эффективности инвестиций в строительство и оснащение производственных площадей под линию обессахаривания мелассы.
Концептуально к проблеме обессахаривания мелассы можно подойти и с другой стороны. Например, добиваясь максимально возможного удаления солей щелочных и щелочноземельных металлов из предшественников мелассы – оттёков предыдущих ступенейкристаллизации,что,нанаш взгляд, является более эффективным. То есть каждый цикл возврата на перекристаллизацию оттёка, предварительно освобождённого от основных мелассообразователей и имеющего более высокую чистоту, позволяет выкристаллизовать большее количество сахарозы и в конечном итоге минимизировать количество получаемой мелассы. Глубокое истощение оттёков сахарного производства и снижение выхода побочного продукта – мелассы – особенно актуально в условиях сложившейся в последние годы экономической ситуации на рынке реализации мелассы, приведшей к ухудшению логистики её движения к потребителю, переизбытку в хранилищах производителя и, соответственно, неоправданным потерям сахара и снижению технико-экономических показателей сахарного завода в целом.
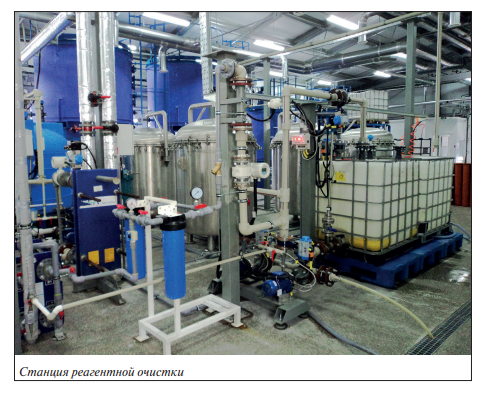
Проблема удаления неорганических несахаров из густых сахарсодержащих полупродуктов решается путём использования электромембранных технологий. В 2017 г. на ОАО «Городейский сахарный
комбинат» была построена и запущена в эксплуатацию технологическая линия по очистке густых полупродуктов сахарного производства от неорганических несахаров (солей щелочных и щелочноземельных металлов) (см. фото). Основной целью строительства данной линии является извлечение дополнительной прибыли из сахарсодержащего сырья с низкой эффективной стоимостью при наличии в нём высокого содержания сахара, обладающего большей эффективной стоимостью в виде готовой продукции.
Технологический процесс очистки густых сахарсодержащих растворов включает в себя две стадии
их обработки– реагентную ибезреагентную и состоит из следующих технологических узлов (рис. 1):
• узел подачи исходного сырья и приготовления рабочего раствора;
• узел реагентной очистки и фильтрации рабочего раствора;
• узел контрольной фильтрации и осветления рабочего раствора;
• узел электрохимической очистки рабочего раствора и получения готового продукта – экстракта;
• узел подачи экстракта в продуктовое отделение..
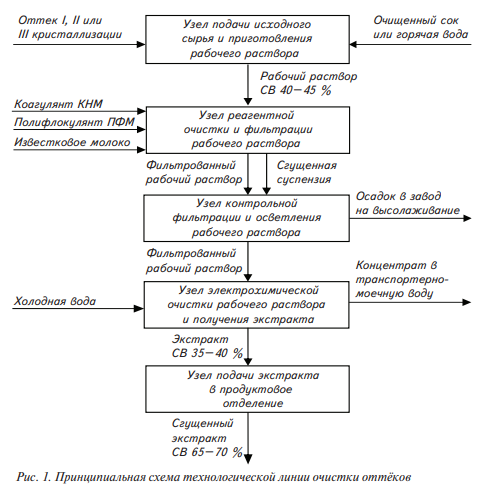
В качестве исходного сырья для приготовления рабочего раствора используются кристаллизационные оттёки (в том числе меласса), разбавленные горячей водой или очищенным диффузионным соком до 40–45 % СВ.
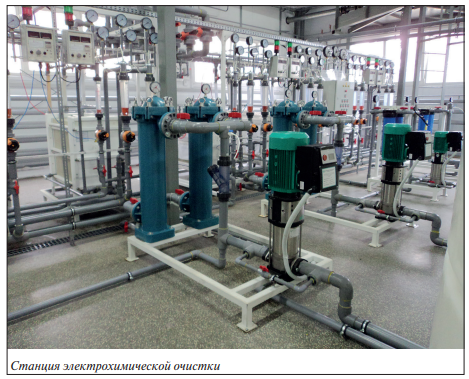
Применяемые на первой стадии реагенты представляют собой сложный композиционный материал, оказывающий комбинированное воздействие на рабочий раствор и включающий систему флокулянтов, коагулянтов, катализаторов. Под влиянием используемого для очистки известкового молока образуются частицы осадка с разветвлённой поверхностью и хорошей адсорбционной активностью по отношению к несахарам, являющиеся одновременно центрами частиц скоагулированного и сформированного осадка, удаляемого посредством отстаивания или центрифугирования. Полученный декантат через ступень контрольной фильтрации и охлаждения направляется на стадию безреагентной (электромембранной) очистки. Суть метода электромембранной очистки заключается в направленном переносе диссоциированных (растворённых солей) ионов из одного раствора в другой под действием разности электрических потенциалов, прикладываемых к электродам, через селективно проницаемые мембраны (рис. 2). Электродиализу подвержены только те вещества, которые при растворении диссоциируют на ионы или образуют заряженные комплексы. Недиссоциирующие вещества (например, сахароза, бетаин, молекулы которых при растворении не несут какого-либо заряда) в электродиализном процессе не участвуют. В результате комплексной электрохимической обработки чистота очищенного рабочего раствора за счёт удаления значительной части несахаров с высокой мелассообразующей способностью повышается на 10– 20 %.
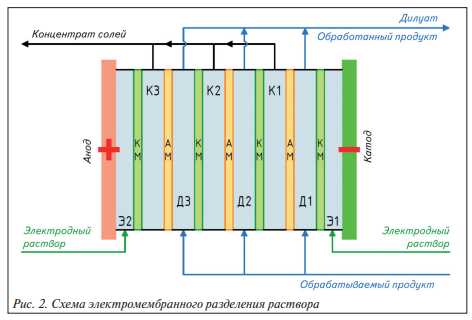
Готовый продукт – это экстракт, в максимальной степени освобождённый от катионов щелочных и щелочноземельных металлов, анионов минеральных кислот и солей (хлориды, сульфаты, фосфаты, нитраты, нитриты) и других органических примесей, с качественными параметрами, отвечающими требованиям ведения технологического процесса кристаллизации сахарозы в условиях сахарного завода. В зависимости от качественных показателей (чистота, цветность) экстракт направляется на уваривание утфеля I, II или III кристаллизации либо на стадию клерования сахаров II и III кристаллизаций. Перед возвратом в кристаллизационное отделение экстракт может быть подвергнут сгущению до содержания сухих веществ 65–70 %.
Приведём некоторые техникоэкономические показатели эксплуатации технологической линии на предприятии ОАО «Городейский сахарный комбинат»:
• производительность линии: 50 т/сут по оттёку II кристаллизации или мелассе;
• коэффициент извлечения сахара: 70–80 %; количество дополнительного сахара: 15–20 т/сут, или 350–400 кг на каждую перерабатываемую тонну мелассы;
• расход электроэнергии: до 1 кВт на 1 кг удаляемых солей;
• расход химических реагентов: до 1,7 м3 /сут;
• расход воды (пароконденсат из ТЭЦ): 5-6 м3на 1 т сахара;
• расход известкового молока: до 1,5 м3 /сут.
Технологическая линия по очистке густых полупродуктов расположена в отдельно стоящем производственном помещении площадью 480 м2 и функционирует в сезон переработки заводом сахарсодержащего сырья (сахарная свёкла, тростниковый сахарсырец) круглосуточно. Численность обслуживающего персонала в период работы линии составляет 10 человек. На строительство нового производственного здания, поставку и монтаж оборудования, подведение коммуникаций затрачено 6 месяцев.
Преимущества нового метода:
• незначительные капитальные затраты;
• небольшие технологические затраты;
• отсутствие неспецифических для сахарного завода отходов;
• возможность встроить в технологическую схему любого сахарного завода;
• возможность регулировать степень извлечения сахарозы из мелассы;
• короткий срок окупаемости.